Table of contents:
Innovative Materials Used in Modern Ball Bearings
Precision Engineering Techniques in Bearing Production
The Impact of Advanced Manufacturing on Bearing Performance
Future Trends in Ball Bearing Technology for Robotics
Innovative Materials Used in Modern Ball Bearings
Modern ball bearings owe much of their efficiency to the advanced materials used in their construction. Traditional steel bearings have evolved to include high-grade material options like ceramic and hybrid ceramic bearings. Ceramic options, such as silicon nitride, are increasingly favored for their lightweight, high-strength characteristics, and corrosion resistance. These materials are especially valuable in robotics where reducing weight without compromising structural integrity is critical. For example, special bearings for robot reducer use high-precision materials that are tailored for demanding operational conditions. This includes bearings that withstand high-frequency shocks and maintain excellent motion control in complex environments, such as the joints of humanoid robots or robot dogs. This leap in materials is helping ball bearing manufacturers create products with exceptional durability, stiffness, and reduced maintenance needs.
Precision Engineering Techniques in Bearing Production
Precision engineering is foundational in ball bearing manufacturing today, particularly when creating components that are vital to a robot's core movements. Advanced machining techniques, including computer numerical control (CNC) machining, ensure precise alignment and surface finishes, allowing bearings to operate with near-zero friction. Furthermore, innovations such as laser texturing and anti-fatigue coating applications enhance the durability and accuracy of bearings under extreme loads. A significant example is noted in the production of RV and harmonic reducer bearings that are specially designed for robotics. These bearings depend on intricate designs, such as cross roller bearing and four-point contact bearings, which can support axial, radial, and torsional loads simultaneously. Bearing supplier are also utilizing automation and AI-driven manufacturing processes to identify defects early, ensuring a higher level of precision and quality control.
The Impact of Advanced Manufacturing on Bearing Performance
The advancements in materials and engineering techniques directly contribute to improved bearing performance in robotics. Bearings today can withstand complex multi-directional loads, provide reliable motion, and enhance long-term accuracy in demanding applications. For robotic joints, such as those found in hips, knees, or arms, these high-performance bearings reduce vibration and noise while increasing torque capabilities. This makes them pivotal in creating robots that mimic human-like movements or react to external stimuli, such as robotic dogs used for advanced tasks. Notably, innovative ball bearing manufacturers focus on creating products with longer lifespans and lightweight structures, helping robots remain agile yet strong. For instance, flexible bearings and harmonic reducer bearings are engineered to deliver unparalleled precision, making them ideal for use in humanoid robotics and automation systems intended for industrial applications.
Future Trends in Ball Bearing Technology for Robotics
The future of ball bearing technology in robotics is set to be marked by significant breakthroughs, heavily influenced by trends in automation and AI. Smart bearings with embedded sensors are becoming a reality, allowing real-time performance monitoring. These sensors can measure parameters such as speed, vibration, and temperature, helping predict failures before they disrupt operations. Ball bearing manufacturers may also leverage advancements in nanotechnology, using nano-coatings to further minimize friction and enhance wear resistance. Another growing trend is the emphasis on environmentally friendly manufacturing processes. Sustainable practices, such as reducing waste and utilizing recyclable materials, are becoming priorities for bearing suppliers. Additionally, custom-designed bearings for specific robotic applications are expected to gain traction as robots continue to diversify in form and function. Bearings will likely become even smaller as robots themselves become more compact, creating opportunities for micro-sized bearing designs. This continual evolution underscores the critical role of advancements in bearing technologies in shaping the future of robotics.
The robotics industry owes much of its progress to the remarkable advancements in ball bearing manufacturing. From innovative materials to precision engineering and the exploration of smart technologies, high-performance bearings have propelled robots into new domains of capability and efficiency. Bearing manufacturers and suppliers continually innovate to meet the unique demands of robotics, helping create solutions for next-generation applications. By leveraging special bearings for robot reducers and other state-of-the-art technologies, robotics engineers and developers can unlock unparalleled possibilities in efficiency, precision, and performance.
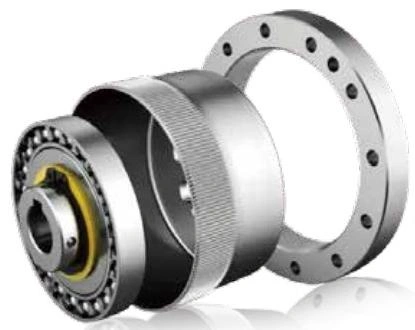
No comments:
Post a Comment