Table of contents:
Understanding the Quality Control Measures in CPP Film Manufacturing
Common Testing Methods to Ensure CPP Film Durability
The Importance of Certifications for CPP Film Manufacturers
How Quality Assurance Impacts the Performance of CPP Films
Understanding the Quality Control Measures in CPP Film Manufacturing
Quality assurance is crucial in the production of cast polypropylene (CPP) plastic films, as these materials are used in sensitive applications such as food packaging, medical products, and textiles. A reliable CPP film manufacturer must implement rigorous quality control measures to ensure product consistency, performance, and safety. This begins with stringent process control during the cast extrusion process, where properties like thickness, clarity, and sealing ability are closely monitored. Advanced production lines, state-of-the-art slitting machines, and meticulous inspections help maintain a uniform finish and superior tear resistance. High standards of hygiene and safety protocols also ensure CPP films meet global regulatory requirements for food-grade and medical-grade materials. Reliable manufacturers often certify their products with relevant certifications such as FDA, MSDS, RoHS, and REACH.
Common Testing Methods to Ensure CPP Film Durability
Testing is a critical component of quality assurance that ensures CPP films meet the durability and performance standards required for their applications. CPP films are subjected to various tests to evaluate their mechanical, thermal, and optical properties. For mechanical durability, tests like tensile strength, tear resistance, and puncture resistance are conducted to confirm that the film can withstand the stresses of manufacturing and usage. Optical clarity tests assess the film’s transparency and gloss, essential for visually appealing packaging. Heat sealability and sealing strength are measured to ensure the film functions flawlessly in high-speed packaging machines. Additionally, barrier properties such as water vapor transmission rates (WVTR) are evaluated to confirm the effectiveness of CPP film in protecting packaged goods. These comprehensive testing protocols make CPP films a reliable solution for packaging needs.
The Importance of Certifications for CPP Film Manufacturers
For a wholesale CPP film manufacturer, obtaining and maintaining certifications is vital to establish credibility and gain customer trust. Certifications like FDA approval are necessary for CPP plastic films used in food and medical packaging, as they verify compliance with health and safety standards. MSDS (Material Safety Data Sheets) and RoHS certifications confirm the material's non-toxic and environmentally safe nature, aligning with increasingly eco-conscious global markets. REACH certification ensures the CPP films conform to European chemical regulations, making them market-ready for international distribution. Certified manufacturers demonstrate their commitment to quality, safety, and sustainability, distinguishing themselves in a competitive marketplace. Customers seeking wholesale CPP films benefit from these guarantees, knowing they're investing in a product that meets rigorous standards.
How Quality Assurance Impacts the Performance of CPP Films
The performance of CPP films is directly linked to the robustness of the quality assurance processes employed by the manufacturer. High-quality CPP films, produced under strict quality assurance guidelines, offer exceptional clarity, excellent sealing properties, and outstanding tear resistance. These characteristics make them ideal for versatile applications such as food packaging, medical film, textiles, and industrial laminations. Quality assurance also enhances the film's compatibility with modern printing methods such as flexographic and rotogravure printing, ensuring consistent results across packaging production lines. Furthermore, sustainable practices in quality assurance facilitate eco-friendly choices, as recyclable CPP films provide a cost-effective and environmentally responsible solution. When manufacturers prioritize quality assurance, customers benefit from reliable products that meet both functional and ethical standards.
The importance of quality assurance in the production of CPP films cannot be overstated. It is the foundation for ensuring high performance, reliability, and sustainability in various applications. Manufacturers who prioritize rigorous quality assurance processes not only deliver superior products but also contribute to a more sustainable and environmentally conscious future. By adhering to these standards, CPP films will continue to meet the growing demands of industries while maintaining their position as a versatile, durable, and eco-friendly packaging solution.
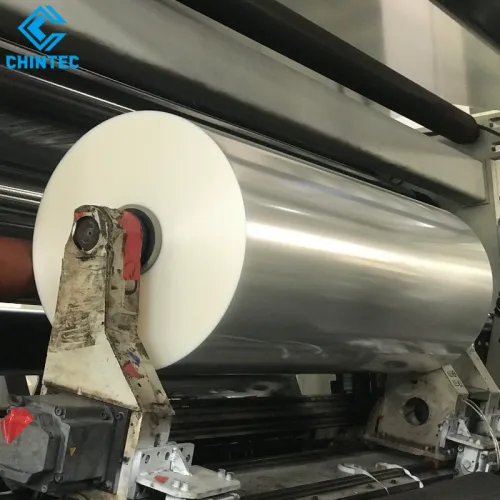
No comments:
Post a Comment